Lean Manufacturing: Descubra os 7 Desperdícios e como eliminá-los
O Lean Manufacturing, também conhecido como Manufatura Enxuta, é uma abordagem sistemática para otimizar os processos produtivos e eliminar desperdícios.
What is Lean Manufacturing?
Lean Manufacturing and its Origins
Lean Manufacturing, also known as Manufatura Enxuta, is a systematic approach to optimizing production processes and eliminating waste. It is a method that originated in Japan, at the Toyota factory, and its main objective is to achieve maximum operational efficiency by reducing production time and minimizing unnecessary costs.
This methodology is based on fundamental principles such as waste elimination, quality improvement, continuous improvement, and respect for people. By implementing Lean Manufacturing, companies seek to create an efficient work environment, maximizing the use of resources, reducing non-value-added activities, and increasing customer satisfaction.
The 7 Wastes of Lean Manufacturing
In Lean Manufacturing, there are seven main types of waste, also known as the 7 wastes of Lean Manufacturing. They are:
1. Superproduction
Producing more than necessary or before it is needed can generate unnecessary costs and increase inventory levels.
2. Waiting
Any time a product, process, or resource is left idle, waiting for a step or activity, is considered waste in the Lean system.
3. Transportation
Excessive movement of products, materials, or information within a company can result in delays, damage, and additional costs.
4. Unnecessary Processing
Activities that are not essential to the final product or service, but consume time and resources, are considered waste.
5. Inventory
Excess unsold inventory represents tied-up capital, storage costs, and potential obsolescence.


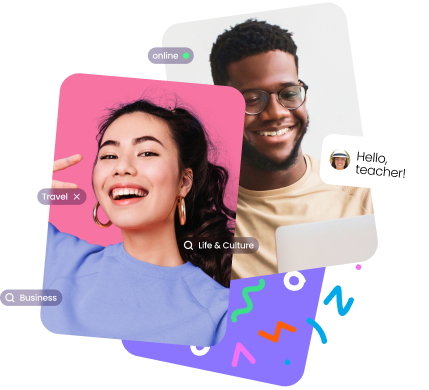
6. Motion
Moving unnecessarily or in a disorganized manner can result in damage, loss of time, and increased costs.
7. Defects
Products or services that do not meet customer expectations, leading to rework, scrap, and dissatisfaction.
By identifying and eliminating these wastes, companies can reduce costs, increase productivity, improve quality, and increase customer satisfaction. To do this, it is necessary to analyze all processes involved, from the supply of raw materials to the delivery of the final product.
How to Identify Wastes in Production Processes
Identifying waste in production processes is essential for the effective implementation of Lean Manufacturing. Through this identification, companies can identify areas that need improvement and eliminate activities that do not add value to the final product or service.
To identify waste, it is important to analyze each step of the production process, from the receipt of raw materials to the delivery of the final product to the customer. Here are some strategies that can be adopted to identify waste:
1. Direct Observation
Direct observation of processes in real-time can reveal unnecessary activities, senseless movements, excessive inventory, among other problems. It is important to observe workflows, waiting times, and any other activity that appears to be off the main goal.
2. Value Stream Mapping
Value Stream Mapping is a powerful tool for visualizing all steps of the process and identifying where waste occurs. This mapping, which can be done through diagrams, helps identify bottlenecks, waiting times, unnecessary movements, and other improvement opportunities.
3. Data Analysis
Data analysis is a more quantitative approach to identify waste. Through data analysis, it is possible to analyze performance indicators, such as cycle time, rework rate, excess inventory quantity, among others. This data can provide valuable insights into waste present in production processes.
4. Employee Feedback
Employees who work directly in the processes have deep knowledge of the challenges and improvement opportunities. Encouraging their feedback, listening to their suggestions, and involving them in waste identification and elimination activities is essential.
By identifying waste in production processes, companies can focus their efforts on eliminating these activities and achieve a more efficient and agile flow.
Strategies to Eliminate the 7 Wastes of Lean Manufacturing
Eliminating the 7 wastes of Lean Manufacturing requires the implementation of effective strategies that aim to optimize production processes, reduce unnecessary costs, and increase the quality of products or services offered by the company. Here are some strategies that can be adopted:
1. Superproduction
One of the strategies to eliminate overproduction is to implement pull production systems, such as Just-in-Time. This means producing what is necessary at the right moment, avoiding the accumulation of inventory and reducing expenses with materials and storage space.
2. Waiting
To eliminate waiting times, it is necessary to optimize the workflow and reduce non-essential activities. This can be done through process analysis and the reorganization of the factory layout, maximizing operational efficiency and minimizing waits between steps.


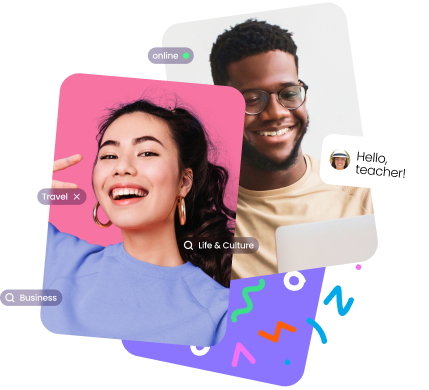
3. Transportation
To reduce unnecessary transportation, it is important to minimize the distances traveled between production areas. This can be done by reevaluating the factory layout, organizing workflows logically, and implementing efficient movement systems, such as the use of carts or conveyors.
4. Unnecessary Processing
The strategy to eliminate unnecessary processing is to review processes and identify activities that do not add value. It is important to focus on the steps that truly contribute to the quality of the final product or service, eliminating any redundant activity.
5. Inventory
To reduce excess inventory, it is essential to implement efficient inventory management systems. This involves analyzing demand, establishing replenishment parameters, and implementing real-time tracking systems, which help ensure adequate inventory levels without excess.
6. Motion
The strategy to eliminate unnecessary motion is to optimize the factory layout, reducing the distance traveled by employees and materials. In addition, the use of appropriate tools and equipment can also contribute to the reduction of excessive movement.
7. Defects
The strategy to eliminate defects involves implementing robust quality control methods, such as real-time inspection, standardization of processes, and adequate training of employees. In addition, it is important to constantly seek continuous improvement, identifying the causes of defects and eliminating them.
By implementing these strategies, companies can achieve more efficient production, reducing waste, optimizing processes, and increasing customer satisfaction.
Take Your Next Step with Lean Manufacturing
Now that you know what Lean Manufacturing is and the 7 wastes, it’s time to discover how to identify these wastes in production processes and the strategies to eliminate them. Let’s go!
The Best Platform to Learn Product Management in Brazil
Awari is the best platform to learn about product management in Brazil. Here you can find courses with live classes, individual mentorship with top professionals in the market, and personalized career support to take your next professional step and learn skills like Data Science, Data Analytics, Machine Learning, and more.
Have you ever thought about learning individually with professionals who work at companies like Nubank, Amazon, and Google? Click here to sign up for Awari and start building the next chapter of your career in data now.
Conclusion
By adopting Lean Manufacturing, companies become more competitive, agile, and prepared to face the challenges of today’s market. It is an approach that aims not only to improve production processes but also to promote a culture of efficiency and innovation, ensuring long-term sustainability and growth.


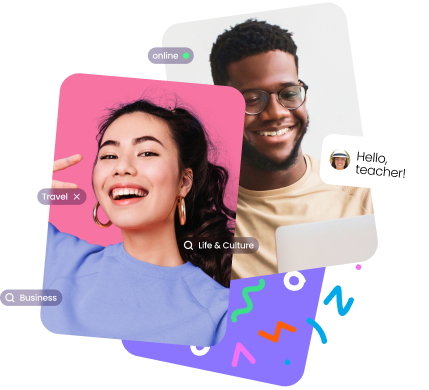