Como aplicar o Lean Manufacturing para reduzir o tempo de espera
Como Aplicar o Lean Manufacturing para Reduzir o Tempo de Espera.
Glossário
Como Aplicar o Lean Manufacturing para Reduzir o Tempo de Espera
Organização do Fluxo de Trabalho
Um dos aspectos fundamentais do Lean Manufacturing é a organização do fluxo de trabalho. Para reduzir o tempo de espera, é essencial mapear o fluxo de valor dos processos e identificar as atividades que não agregam valor ao produto final. Através desse mapeamento, pode-se identificar gargalos e eliminar etapas desnecessárias, otimizando assim o fluxo de trabalho.
Alguns passos podem ser seguidos para organizar o fluxo de trabalho de forma eficiente:
- Identificar as atividades que agregam valor: Essas são as atividades que têm impacto direto no produto final e que são consideradas essenciais pelos clientes. Ao identificar essas atividades, é possível priorizá-las e garantir que sejam executadas de forma eficiente.
- Eliminar atividades que não agregam valor: Essas são as atividades que consomem recursos e tempo, mas não contribuem para a qualidade do produto final. Identificar e eliminar essas atividades é essencial para reduzir o tempo de espera.
Otimização dos Processos de Produção
Outra estratégia importante para reduzir o tempo de espera é a otimização dos processos de produção. Isso envolve identificar e eliminar gargalos, reduzir o tempo de setup, implementar fluxos contínuos de produção e melhorar a flexibilidade.
Algumas técnicas e ferramentas que podem ser utilizadas para otimizar os processos de produção incluem:
- Single Minute Exchange of Die (SMED): Uma metodologia que visa reduzir o tempo de setup das máquinas, possibilitando a troca rápida de ferramentas e reduzindo assim os tempos de espera.
- Fluxo Contínuo: Implementar um fluxo contínuo de produção, onde as atividades são realizadas de forma sequencial e sem interrupções, evitando assim os tempos de espera entre as etapas.
- Kanban: Uma ferramenta de controle de produção que ajuda a evitar excessos e garantir que os materiais necessários estejam disponíveis no momento adequado, reduzindo assim os tempos de espera.
Eliminação de Desperdícios
Um dos princípios fundamentais do Lean Manufacturing é a eliminação de desperdícios. Para reduzir o tempo de espera, é importante identificar e eliminar qualquer atividade que não agregue valor ao produto final.
Os principais tipos de desperdícios que podem causar tempos de espera desnecessários são:
- Espera: Tempo gasto esperando por insumos, equipamentos ou instruções.
- Movimentação: Movimentação excessiva de materiais ou pessoas, o que aumenta o tempo necessário para a realização das atividades.
- Estoque excessivo: Manter altos níveis de estoque pode resultar em tempos de espera desnecessários, pois é preciso aguardar o processamento desses estoques antes de avançar para a próxima etapa.
- Processamento desnecessário: Realizar atividades que não agregam valor ao produto final, como retrabalho ou validações excessivas.
Melhoria Contínua através da Monitorização e Análise de Dados
A melhoria contínua é um pilar do Lean Manufacturing. Para reduzir o tempo de espera, é fundamental monitorar e analisar constantemente os dados relacionados ao processo produtivo, buscando identificar oportunidades de melhoria.


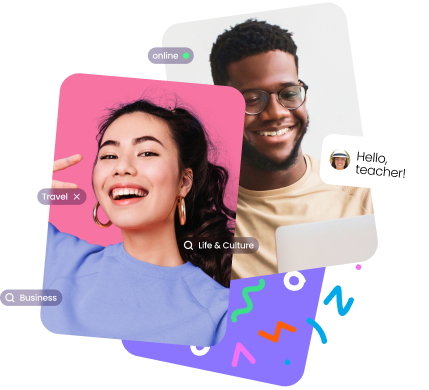
Algumas ferramentas que podem ser utilizadas para realizar essa análise são:
- Gráficos de Controle: Permitem visualizar as variações nos processos e identificar padrões que podem impactar no tempo de espera.
- Análise de Valor Agregado: Com essa técnica, é possível identificar as atividades que realmente agregam valor ao produto final e aquelas que podem ser eliminadas ou otimizadas.
- Ciclo PDCA (Plan-Do-Check-Act): Uma metodologia que incentiva a experimentação e a busca constante por melhorias através do planejamento, execução, verificação e ação.
Conclusão
A aplicação dos princípios do Lean Manufacturing pode ser extremamente útil para reduzir o tempo de espera em processos produtivos. Ao organizar o fluxo de trabalho, otimizar os processos, eliminar desperdícios e buscar melhorias contínuas, as empresas podem aumentar a eficiência, reduzir custos e oferecer um melhor atendimento aos clientes. Portanto, é fundamental compreender e aplicar o Lean Manufacturing para reduzir o tempo de espera de forma eficaz.
Organização do Fluxo de Trabalho
Um aspecto fundamental para reduzir o tempo de espera em um ambiente de produção é a organização do fluxo de trabalho. É essencial entender o fluxo de valor dos processos e identificar as atividades que não agregam valor ao produto final, pois são justamente essas atividades que podem causar atrasos e tempos de espera desnecessários.
Para organizar o fluxo de trabalho de forma eficiente e reduzir os tempos de espera, podem ser seguidos alguns passos importantes:
- Identificar as atividades que agregam valor: Essas atividades são as que efetivamente contribuem para a criação do produto final e são valorizadas pelos clientes. Ao identificá-las, é possível priorizá-las e garantir que sejam executadas de maneira eficiente, reduzindo os tempos de espera.
- Eliminar atividades que não agregam valor: Muitas vezes, existem atividades que consomem tempo e recursos, mas não agregam valor ao produto final. Identificar essas atividades e eliminá-las é fundamental para reduzir os tempos de espera. Nesse sentido, o Lean Manufacturing oferece diversas ferramentas e técnicas para identificar e eliminar os desperdícios, como o Mapeamento do Fluxo de Valor (Value Stream Mapping), que permite visualizar o fluxo de valor e identificar possíveis áreas de melhoria.
- Estabelecer um fluxo contínuo: Um fluxo contínuo de trabalho é essencial para reduzir os tempos de espera. Isso significa que as atividades devem ser realizadas em sequência, sem interrupções desnecessárias. Para alcançar esse objetivo, é importante eliminar gargalos e garantir que o trabalho flua de forma contínua, sem acumular estoques intermediários ou aguardar etapas de validação.
- Aproximar as equipes: A proximidade física das equipes pode contribuir para reduzir os tempos de espera. Quando as equipes estão fisicamente próximas e podem se comunicar facilmente, é mais fácil coordenar as atividades, reduzir os atrasos e tomar decisões rápidas.
Ao aplicar o Lean Manufacturing para reduzir o tempo de espera através da organização do fluxo de trabalho, é possível otimizar o processo produtivo, eliminar desperdícios e aumentar a eficiência. Essa melhoria no fluxo de trabalho resulta em entregas mais rápidas, menor quantidade de produtos em espera e satisfação dos clientes.
Otimização dos Processos de Produção
Uma das chaves para reduzir o tempo de espera é otimizar os processos de produção. Através da identificação e eliminação de gargalos, redução do tempo de setup, implementação de fluxos contínuos e aumento da flexibilidade, é possível acelerar o ritmo de produção e reduzir o tempo necessário para atender a demanda.
Diversas técnicas e ferramentas podem ser utilizadas para otimizar os processos de produção. Algumas delas incluem:
- Single Minute Exchange of Die (SMED): Esta metodologia visa reduzir o tempo de setup das máquinas, permitindo a rápida troca de ferramentas e reduzindo os tempos de espera entre as mudanças de produção. Ao reduzir esse tempo, é possível aumentar a flexibilidade da produção e responder rapidamente às mudanças na demanda.
- Fluxo Contínuo: A implementação de um fluxo contínuo na produção é fundamental para eliminar tempos de espera desnecessários. Ao organizar o processo produtivo de forma sequencial e eliminar as interrupções, é possível manter um ritmo de produção constante, sem acúmulo de estoques intermediários e sem esperas entre as etapas.
- Kanban: O sistema Kanban é uma ferramenta de controle da produção que permite gerenciar o fluxo de materiais e informações de forma eficiente. Com o uso de cartões Kanban, é possível controlar a quantidade de materiais em estoque, evitar excessos e garantir que os materiais necessários estejam disponíveis no momento adequado, reduzindo assim os tempos de espera.
A otimização dos processos de produção é fundamental para reduzir os tempos de espera. Ao implementar técnicas como o SMED, fluxo contínuo e utilizar o sistema Kanban, é possível aumentar a eficiência, reduzir a espera por materiais e entregar produtos de forma mais rápida aos clientes.
Eliminação de Desperdícios
A eliminação de desperdícios é um dos principais princípios do Lean Manufacturing. Ao identificar e eliminar atividades que não agregam valor ao produto final, é possível reduzir o tempo de espera e aumentar a eficiência do processo produtivo.


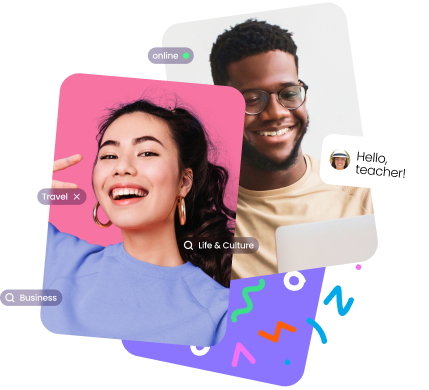
Existem diferentes tipos de desperdícios que podem causar tempos de espera desnecessários, tais como:
- Espera: Tempo gasto aguardando a chegada de insumos, informações ou instruções. A espera pode ocorrer quando um processo depende da conclusão de outro ou quando há atrasos no fornecimento de materiais.
- Movimentação excessiva: Movimentar-se de maneira desnecessária dentro do processo produtivo pode aumentar o tempo de execução das atividades e causar atrasos. A análise do layout dos equipamentos e das áreas de trabalho pode ajudar a identificar áreas de movimentação excessiva e reduzir os tempos de espera.
- Estoque excessivo: Manter estoques em excesso pode levar a tempos de espera desnecessários. O estoque excessivo pode ocorrer devido a compras em grande quantidade, produção em excesso ou falhas de comunicação dentro da cadeia de suprimentos. Reduzir o estoque excessivo pode ser uma estratégia eficaz para reduzir o tempo de espera.
- Processamento desnecessário: Realizar atividades que não agregam valor ao produto final, como retrabalho ou validações excessivas, é um desperdício que pode aumentar o tempo de espera. Identificar e eliminar processos desnecessários é essencial para reduzir o tempo necessário para a produção.
Melhoria Contínua através da Monitorização e Análise de Dados
A melhoria contínua é um princípio essencial do Lean Manufacturing. Através da monitorização e análise de dados, é possível identificar oportunidades de melhoria, reduzir os tempos de espera e alcançar um processo produtivo mais eficiente.
Algumas ferramentas e técnicas que podem ser utilizadas para a melhoria contínua incluem:
- Gráficos de Controle: Essas ferramentas permitem monitorar e visualizar as variações nos processos de produção. Ao analisar os gráficos de controle, é possível identificar padrões e tendências que podem indicar problemas e ajudar a tomar ações corretivas para reduzir os tempos de espera.
- Análise de Valor Agregado: A análise de valor agregado permite identificar as atividades que efetivamente agregam valor ao produto final. Ao analisar e entender as atividades que agregam valor, é possível focar os esforços na redução de tempos de espera e eliminar desperdícios em atividades que não agregam valor.
- Ciclo PDCA (Plan-Do-Check-Act): O ciclo PDCA é uma metodologia que enfatiza a importância da experimentação e da aprendizagem contínua. Ao planejar, executar, verificar e agir, é possível identificar oportunidades de melhoria, implementar mudanças e monitorar os resultados para alcançar uma redução efetiva dos tempos de espera.
A melhoria contínua é um processo constante que visa aprimorar continuamente o processo produtivo. Através da monitorização e análise de dados, o Lean Manufacturing oferece ferramentas e técnicas que permitem identificar áreas de melhoria para reduzir os tempos de espera e obter um processo de produção mais eficiente e ágil.
Conclusão
A aplicação dos princípios do Lean Manufacturing, como a organização do fluxo de trabalho, otimização dos processos de produção, eliminação de desperdícios e busca por melhoria contínua, pode ser altamente eficaz para reduzir o tempo de espera em processos produtivos. Ao implementar essas estratégias, as empresas podem aumentar a eficiência, reduzir custos e entregar produtos de forma mais rápida aos clientes, atendendo suas expectativas. Portanto, entender e aplicar o Lean Manufacturing é fundamental para reduzir o tempo de espera e melhorar a competitividade no mercado.
Awari é a melhor plataforma para aprender sobre gestão de produtos no Brasil.
Aqui você encontra cursos com aulas ao vivo, mentorias individuais com os melhores profissionais do mercado e suporte de carreira personalizado para dar seu próximo passo profissional e aprender habilidades como Data Science, Data Analytics, Machine Learning e mais.
Já pensou em aprender de maneira individualizada com profissionais que atuam em empresas como Nubank, Amazon e Google? Clique aqui para se inscrever na Awari e começar a construir agora mesmo o próximo capítulo da sua carreira em dados.


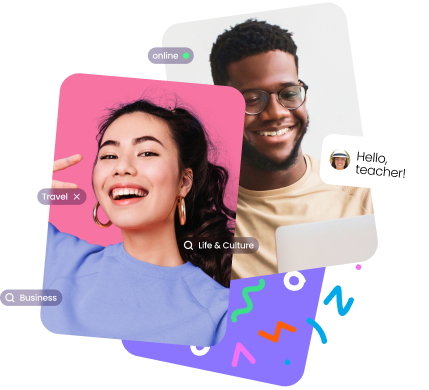