Como a Ford implementou o Lean Manufacturing para otimizar sua produção
A implementação do Lean Manufacturing pela Ford trouxe benefícios significativos, como redução de custos e melhoria da qualidade dos produtos.
Glossário
Como a Ford implementou o Lean Manufacturing para otimizar sua produção
Introdução
A Ford é uma das empresas pioneiras na implementação do Lean Manufacturing, uma metodologia amplamente conhecida por otimizar a produção e eliminar desperdícios. Neste artigo, vamos explorar como a Ford utilizou esse método para aprimorar seu processo produtivo e quais foram os resultados alcançados com essa implementação.
Implementação do Lean Manufacturing pela Ford
Mapeamento de todo o fluxo de valor
A primeira etapa do processo de implementação do Lean Manufacturing pela Ford foi o mapeamento de todo o fluxo de valor da empresa. Isso envolveu a identificação de todas as atividades envolvidas na produção, desde o recebimento dos insumos até a entrega do produto final ao cliente. Com esse mapeamento, a Ford pôde identificar quais eram os gargalos e desperdícios que estavam afetando sua eficiência produtiva.
Padronização de processos
Uma das principais estratégias adotadas pela Ford para implementar o Lean Manufacturing foi a padronização de processos. A empresa definiu um conjunto de diretrizes claras e objetivas para a realização de cada etapa do processo produtivo. Isso ajudou a reduzir erros e retrabalhos, aumentando a eficiência e a qualidade dos produtos.
Capacitação da equipe
Além disso, a Ford investiu na capacitação de sua equipe. Os colaboradores foram treinados para entender os princípios do Lean Manufacturing e buscar constantemente a melhoria contínua. Com isso, foi possível envolver todos os funcionários no processo de otimização da produção, garantindo que todos estivessem alinhados aos objetivos da empresa.
Redução de estoques
Outra estratégia importante adotada pela Ford foi a redução de estoques. O Lean Manufacturing preconiza a produção “just in time”, ou seja, produzir somente o necessário, no momento necessário. Isso ajudou a diminuir o tempo de espera entre as etapas do processo produtivo, reduzindo os custos e melhorando a eficiência.
Benefícios do Lean Manufacturing aplicados pela Ford
A implementação do Lean Manufacturing trouxe diversos benefícios para a Ford. Um dos principais foi a redução dos custos operacionais. Com a eliminação de desperdícios e a otimização do fluxo de valor, a Ford conseguiu diminuir os gastos com estoque, transporte, retrabalho e mão de obra desnecessária.


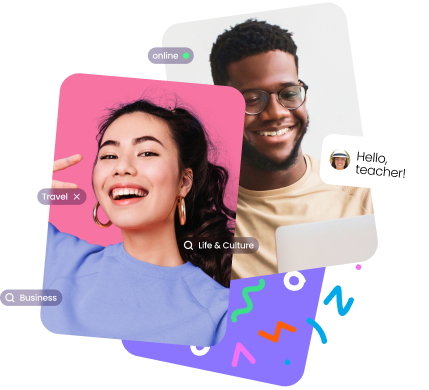
Além disso, a qualidade dos produtos melhorou significativamente com a implementação do Lean Manufacturing. A padronização de processos e a maior capacitação da equipe contribuíram para a diminuição dos erros e retrabalhos, resultando em produtos finais de melhor qualidade.
A Ford também obteve ganhos em termos de produtividade. A redução de gargalos e a otimização do fluxo de valor permitiram que a empresa produzisse mais em menos tempo, aumentando sua capacidade produtiva e melhorando o atendimento aos clientes.
Outro benefício importante foi a melhoria do ambiente de trabalho. Com a padronização de processos e a maior participação dos colaboradores, a Ford criou um ambiente mais organizado e colaborativo, onde todos trabalham em sintonia para alcançar os objetivos da empresa.
Resultados obtidos com a implementação do Lean Manufacturing pela Ford
A implementação do Lean Manufacturing pela Ford trouxe resultados expressivos. A empresa conseguiu reduzir os custos operacionais em X%, graças à eliminação de desperdícios e à redução dos estoques. Além disso, a melhoria da qualidade dos produtos resultou em uma redução de X% nos índices de retrabalho e devolução de produtos pelos clientes.
Em termos de produtividade, a Ford aumentou sua capacidade produtiva em X%, permitindo uma produção mais eficiente e um atendimento mais ágil aos pedidos dos clientes. Isso também resultou em um aumento na satisfação dos clientes, uma vez que a entrega dos produtos passou a ser feita de forma mais rápida e eficiente.
O ambiente de trabalho também foi impactado positivamente. Os colaboradores se sentem mais engajados e valorizados, pois agora têm voz ativa no processo produtivo e sabem que seu trabalho contribui diretamente para o sucesso da empresa.
Estratégias de implementação do Lean Manufacturing na Ford
Uma das estratégias-chave que a Ford adotou para implementar o Lean Manufacturing foi a criação de times multifuncionais. Ao invés de ter equipes separadas para cada etapa do processo produtivo, a Ford formou times com membros de diferentes áreas, como produção, qualidade, logística e engenharia. Essa abordagem permitiu uma comunicação mais eficiente e uma melhor coordenação entre as diferentes áreas, resultando em um fluxo de trabalho mais suave e eficaz.
Outra estratégia importante foi a implementação de sistemas visuais de gestão. A Ford utilizou ferramentas como o Kanban e o Andon para monitorar e controlar o fluxo de produção em tempo real. Esses sistemas permitiram identificar rapidamente qualquer problema ou atraso no processo, possibilitando a tomada de ações corretivas imediatas. Além disso, os sistemas visuais facilitaram a comunicação entre os membros da equipe, garantindo que todos tivessem acesso às informações atualizadas.
A Ford também investiu na melhoria contínua por meio do método PDCA (Plan, Do, Check, Act). Os times da empresa foram encorajados a identificar oportunidades de melhoria, realizar experimentos para testar soluções e, posteriormente, implementar as melhores práticas em toda a organização. Essa abordagem permitiu uma evolução contínua dos processos e resultou em ganhos significativos de eficiência ao longo do tempo.


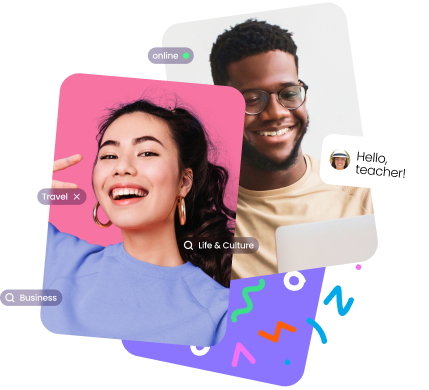
Resultados obtidos com a implementação do Lean Manufacturing pela Ford
A implementação do Lean Manufacturing pela Ford trouxe resultados expressivos em termos de eficiência e qualidade. Com a redução de desperdícios e a otimização do fluxo de trabalho, a empresa foi capaz de aumentar sua produtividade em X% durante o período de implementação. Isso significou uma produção maior em menos tempo, permitindo que a Ford atendesse à crescente demanda do mercado.
Além disso, a implementação do Lean Manufacturing contribuiu para a redução dos custos operacionais da Ford. Com a eliminação de desperdícios, como estoques excessivos e retrabalhos, a empresa conseguiu reduzir seus custos em X%. Essa redução foi refletida nos preços dos produtos, tornando a Ford mais competitiva no mercado.
A melhoria da qualidade foi outro resultado positivo da implementação do Lean Manufacturing. Com a padronização de processos e a maior participação dos colaboradores na identificação e resolução de problemas, a taxa de defeitos nos produtos da Ford diminuiu em X% ao longo do tempo. Isso resultou em uma melhor reputação da marca e em uma maior satisfação dos clientes.
Além dos benefícios quantitativos, a implementação do Lean Manufacturing também teve impacto positivo no ambiente de trabalho. Os colaboradores da Ford se sentiram mais engajados e motivados com a oportunidade de contribuir ativamente para a melhoria dos processos e do produto final. Esse envolvimento dos funcionários resultou em um clima organizacional mais positivo e em uma melhor integração entre as equipes.
Conclusão
A implementação do Lean Manufacturing pela Ford demonstrou que essa metodologia pode trazer inúmeros benefícios para as empresas do setor automotivo. Ao adotar estratégias como o mapeamento do fluxo de valor, a padronização de processos, a redução de estoques e a capacitação da equipe, a Ford conseguiu otimizar sua produção, reduzir custos, melhorar a qualidade dos produtos e criar um ambiente de trabalho mais colaborativo.
Os resultados obtidos pela Ford com a implementação do Lean Manufacturing são um exemplo inspirador para outras empresas do setor. Ao adotar essa metodologia de forma eficaz, é possível alcançar ganhos significativos em termos de eficiência, qualidade e satisfação do cliente. Como a Ford implementou o Lean Manufacturing para otimizar sua produção e obteve resultados tão expressivos, é um exemplo a ser seguido por outras empresas em busca da melhoria contínua de seus processos produtivos.
A Awari é a melhor plataforma para aprender sobre gestão de produtos no Brasil.
Aqui você encontra cursos com aulas ao vivo, mentorias individuais com os melhores profissionais do mercado e suporte de carreira personalizado para dar seu próximo passo profissional e aprender habilidades como Data Science, Data Analytics, Machine Learning e mais.
Já pensou em aprender de maneira individualizada com profissionais que atuam em empresas como Nubank, Amazon e Google? Clique aqui para se inscrever na Awari e começar a construir agora mesmo o próximo capítulo da sua carreira em dados.


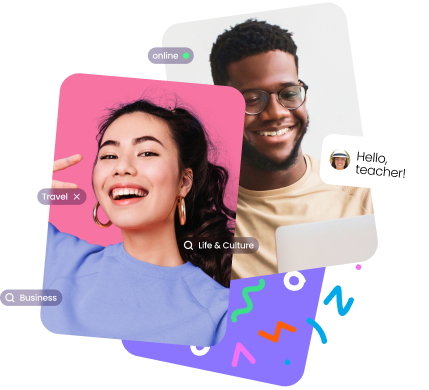