As 8 perdas mortais do Lean Manufacturing: como evitá-las e aumentar sua eficiência
Descubra como evitar as 8 perdas mortais do Lean Manufacturing e aumentar sua eficiência.
Glossário
As perdas mortais do Lean Manufacturing: como evitá-las e aumentar sua eficiência
Introdução
O Lean Manufacturing, também conhecido como manufatura enxuta, é um sistema de gestão que tem como objetivo eliminar desperdícios e otimizar os processos produtivos. No entanto, existem oito perdas mortais que podem prejudicar a eficiência e a produtividade de uma empresa. Neste artigo, vamos explorar essas perdas e discutir como evitá-las, a fim de aumentar a eficiência do Lean Manufacturing.
As 8 perdas mortais do Lean Manufacturing são:
1. Transporte
A movimentação excessiva de materiais ou produtos entre as diferentes etapas do processo produtivo pode levar a atrasos, danos e custos adicionais. Para eliminar essa perda, é importante analisar a logística interna da empresa, buscar a localização mais eficiente dos produtos e utilizar sistemas de transporte adequados.
2. Estoque
O excesso de estoque pode resultar em custos adicionais, obsolescência e desperdício de espaço. É essencial implementar um sistema de gestão de estoque eficiente, que leve em consideração a demanda real e minimize a quantidade de produtos armazenados.
3. Movimentação
O deslocamento desnecessário de pessoas e equipamentos dentro do ambiente de trabalho é uma perda que pode ser evitada com a revisão dos layout dos processos e a busca por formas mais eficientes de organização.


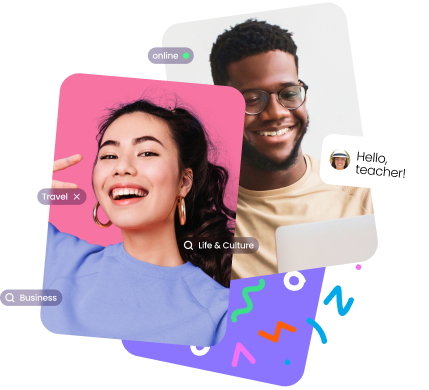
4. Espera
A espera por materiais, informações ou decisões pode resultar em atrasos e interrupções no fluxo produtivo. É importante identificar os gargalos que causam essas esperas e implementar soluções para agilizar o processo.
5. Superprodução
Produzir mais do que o necessário gera estoques excessivos, desperdício de recursos e criação de produtos fora de especificação. Para evitar essa perda, é fundamental alinhar a produção com a demanda real do mercado.
6. Processamento excessivo
Realizar etapas ou processos desnecessários ou mais complexos do que o necessário resulta em custos e tempo adicionais. Simplificar os processos, eliminar etapas desnecessárias e investir em tecnologias mais eficientes são formas de evitar essa perda.
7. Defeitos
A produção de produtos com defeitos resulta em retrabalho, desperdício de tempo e recursos, além de insatisfação dos clientes. Implementar sistemas de controle de qualidade eficazes e treinar os colaboradores para evitar erros são medidas essenciais.
8. Subutilização do talento humano
Não aproveitar todo o potencial dos colaboradores é uma perda que pode afetar tanto a qualidade quanto a eficiência dos processos. É importante envolver os funcionários em projetos de melhoria contínua, ouvir suas sugestões e investir em seu desenvolvimento profissional.
Práticas para evitar essas perdas mortais e aumentar a eficiência do Lean Manufacturing:
- Implementar técnicas de gestão visual, como o uso de quadros kanban, para monitorar e controlar o fluxo de produção.
- Realizar análises de valor para identificar etapas ou processos que não agregam valor ao produto final e eliminá-los.
- Investir em treinamentos e capacitação dos colaboradores, buscando o constante aprimoramento das habilidades e conhecimentos.
- Adotar um sistema de gestão de qualidade, como o Six Sigma, para reduzir a ocorrência de defeitos e melhorar a satisfação dos clientes.
- Implementar um sistema de sugestões e ideias, no qual os colaboradores possam contribuir com melhorias e soluções para eliminar as perdas.
Em resumo, as 8 perdas mortais do Lean Manufacturing representam os principais obstáculos para a eficiência e produtividade de uma empresa. No entanto, ao identificá-las e adotar medidas para evitá-las, é possível alcançar uma gestão mais eficiente, eliminar desperdícios e aumentar a competitividade no mercado. Invista no Lean Manufacturing e alcance resultados incríveis para o seu negócio.
Reduzindo os desperdícios de movimentação no Lean Manufacturing
A movimentação excessiva de materiais e produtos dentro do ambiente de trabalho é uma das perdas mortais do Lean Manufacturing. Esse desperdício não só consome tempo e recursos, mas também pode resultar em danos aos produtos e atrasos nos processos. Para reduzir efetivamente os desperdícios de movimentação, algumas práticas podem ser adotadas:


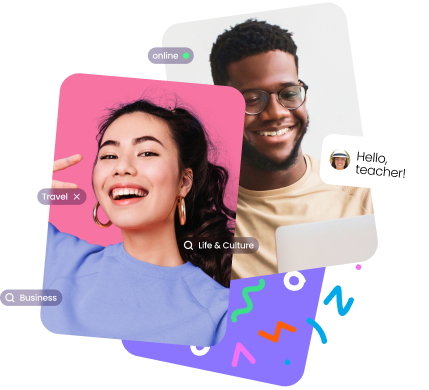
- Reavaliação do layout: A disposição física dos equipamentos, máquinas e estoques deve ser planejada de forma estratégica, buscando minimizar as distâncias percorridas pelos colaboradores e otimizar o fluxo de trabalho.
- Implementação de fluxo contínuo: Ao estabelecer um fluxo contínuo no processo produtivo, é possível eliminar movimentações desnecessárias e otimizar a sequência das atividades. Isso requer um planejamento cuidadoso e a sincronia entre as etapas para evitar gargalos.
- Padronização: A padronização de processos e procedimentos é uma forma eficiente de reduzir os desperdícios de movimentação. Ao estabelecer diretrizes claras para as atividades, é possível evitar movimentos desnecessários e alcançar uma maior eficiência operacional.
- Utilização de equipamentos adequados: A escolha de equipamentos e ferramentas adequadas pode contribuir para a redução da movimentação de materiais. A utilização de carrinhos, esteiras e dispositivos de transporte eficientes pode agilizar o processo e minimizar a necessidade de movimentação manual.
Otimizando o tempo de espera e minimizando a perda de tempo no Lean Manufacturing
O tempo de espera pode ser um grande vilão na eficiência do processo produtivo. Atrasos, paradas e ociosidade podem resultar em perdas significativas de tempo e recursos. Para otimizar o tempo de espera e minimizar a perda de tempo no Lean Manufacturing, algumas estratégias podem ser aplicadas:
- Análise da capacidade produtiva: É fundamental entender a capacidade produtiva da empresa e o tempo necessário para cada etapa do processo. Com base nessa análise, é possível identificar gargalos e tomar medidas para aumentar a eficiência.
- Implementação de Kanban: O sistema Kanban é uma metodologia visual que permite controlar o fluxo de produção. Por meio de cartões ou painéis, é possível acompanhar o progresso das atividades, identificar gargalos e agilizar o processo.
- Sincronização das atividades: A sincronização das atividades é essencial para minimizar o tempo de espera. Isso significa que as etapas do processo devem ser coordenadas e executadas de forma sequencial, evitando ociosidade e paradas desnecessárias.
- Melhoria contínua: O Lean Manufacturing preza pela busca constante por melhorias e eliminação de desperdícios. Através de ferramentas como o Kaizen, é possível envolver os colaboradores na identificação de oportunidades de redução de tempo de espera e implementar soluções eficientes.
A utilização do Lean Manufacturing como metodologia de gestão permite a identificação e eliminação das oito perdas mortais, incluindo as perdas relacionadas à movimentação excessiva e ao tempo de espera. Ao adotar práticas eficientes para reduzir desperdícios de movimentação e minimizar o tempo de espera, as empresas podem aumentar sua eficiência, produtividade e competitividade no mercado.
Em síntese, é essencial que as organizações estejam atentas às perdas mortais do Lean Manufacturing e adotem medidas para evitá-las. As práticas de redução de desperdícios de movimentação e otimização do tempo de espera são fundamentais para alcançar uma gestão mais eficiente e garantir um processo produtivo ágil e sem perdas desnecessárias. Ao implementar essas estratégias, as empresas podem maximizar sua eficiência e obter resultados significativos em seus processos de produção.
A Awari é a melhor plataforma para aprender sobre gestão de produtos no Brasil.
Aqui você encontra cursos com aulas ao vivo, mentorias individuais com os melhores profissionais do mercado e suporte de carreira personalizado para dar seu próximo passo profissional e aprender habilidades como Data Science, Data Analytics, Machine Learning e mais.
Já pensou em aprender de maneira individualizada com profissionais que atuam em empresas como Nubank, Amazon e Google? Clique aqui para se inscrever na Awari e começar a construir agora mesmo o próximo capítulo da sua carreira em dados.


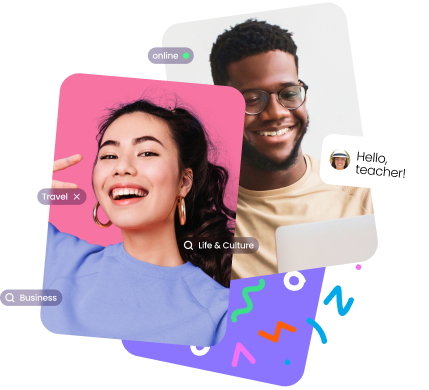