9 desperdícios no Lean Manufacturing: como evitá-los e aumentar a eficiência
Descubra como identificar e eliminar os 9 desperdícios no Lean Manufacturing para otimizar processos e alcançar eficiência.
Glossário
Identificação dos desperdícios no Lean Manufacturing:
1. Superprodução:
Produzir mais do que a demanda do mercado requer resulta em desperdício de recursos, espaço e tempo. É necessário adequar a produção à demanda para evitar estoques excessivos e reduzir custos.
2. Espera:
Tempo de espera entre as etapas do processo produtivo ou por falta de materiais ou informações pode levar a grandes atrasos e desperdício de tempo. É importante reduzir ao máximo esses tempos de espera para aumentar a eficiência e diminuir prazos de entrega.
3. Transporte:
Movimentação desnecessária de materiais ou produtos ao longo da cadeia produtiva pode resultar em danos, perdas e desperdício de tempo. Uma análise cuidadosa dos fluxos de transporte pode ajudar a reduzir essas atividades e otimizar o processo.
4. Processamento desnecessário:
Realizar atividades ou operações que não agregam valor ao produto final é um desperdício significativo. Identificar e eliminar essas etapas desnecessárias é essencial para a eficiência do processo produtivo.
5. Estoque excessivo:
Manter estoques em excesso resulta em altos custos de armazenagem, obsolescência e dificuldades na identificação de problemas. É importante garantir um controle adequado de estoques para evitar desperdícios e otimizar a produção.
6. Movimentação excessiva:
Deslocamentos desnecessários, seja de pessoas, equipamentos ou materiais, são desperdícios que podem ser eliminados com uma análise criteriosa do leiaute da planta fabril e da organização do fluxo de trabalho.
7. Defeitos:
Produtos defeituosos resultam em retrabalho, perda de material e insatisfação do cliente. É essencial investir em controle de qualidade para evitar desperdícios causados por defeitos.
8. Habilidades subutilizadas:
Não aproveitar o máximo das habilidades e conhecimentos dos colaboradores é um desperdício no Lean Manufacturing. É fundamental valorizar e desenvolver a capacidade de cada membro da equipe.


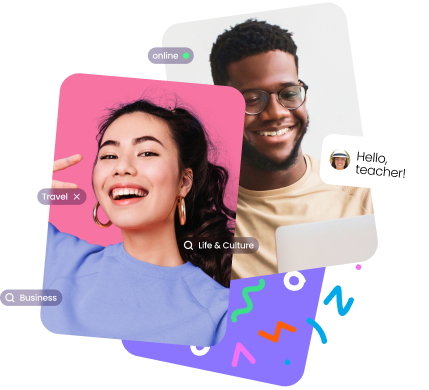
9. Mudanças de setup:
Tempo excessivo gasto em mudanças de configuração de máquinas ou equipamentos resulta em atrasos e perda de produtividade. É importante buscar formas de reduzir o tempo de setup para otimizar a produção.
Como evitar os desperdícios no Lean Manufacturing e aumentar a eficiência:
Agora que conhecemos os principais desperdícios no Lean Manufacturing, é fundamental entender como evitá-los e aumentar a eficiência das operações. A seguir, apresentaremos algumas estratégias e práticas que podem ser adotadas para evitar esses desperdícios:
1. Implementar o Sistema Kanban:
O Kanban é uma ferramenta visual que auxilia no controle de produção e no fluxo contínuo de materiais, permitindo que a produção seja adequada à demanda. Com a utilização do Kanban, é possível evitar a superprodução e reduzir os estoques, aumentando a eficiência e a rapidez nas entregas.
2. Adotar o Just-In-Time (JIT):
O Just-In-Time é um sistema de produção que busca eliminar desperdícios ao produzir exatamente a quantidade necessária no momento necessário, evitando estoques em excesso. Essa abordagem reduz o risco de obsolescência e aumenta a agilidade do processo produtivo.
3. Aplicar a metodologia 5S:
O 5S é uma metodologia que visa organizar o ambiente de trabalho de forma eficiente, eliminando itens desnecessários, padronizando processos e mantendo a limpeza e a ordem no local de trabalho. Essa metodologia contribui para reduzir desperdícios como transporte desnecessário e movimentação excessiva.
4. Investir em treinamento e capacitação dos colaboradores:
Ao desenvolver as habilidades e conhecimentos dos colaboradores, é possível aproveitar melhor a capacidade de cada um e evitar a subutilização de suas competências. Investir em treinamentos e capacitação também contribui para reduzir os erros e defeitos no processo produtivo.
5. Realizar análise de valor:
A análise de valor consiste em realizar uma avaliação criteriosa das atividades do processo produtivo, identificando aquelas que realmente agregam valor ao produto final. Com essa análise, é possível eliminar ou reduzir etapas desnecessárias, evitando o processamento desnecessário.
6. Implementar manutenção preventiva:
A manutenção preventiva visa realizar intervenções programadas nas máquinas e equipamentos, evitando paradas inesperadas e perdas de produção. Ao manter os equipamentos em bom estado, é possível reduzir tempo de setup e aumentar a eficiência.
Estratégias para eliminar os desperdícios no Lean Manufacturing e otimizar processos:
Eliminar os desperdícios no Lean Manufacturing e otimizar os processos é um desafio constante para as empresas que buscam a eficiência máxima em suas operações. Para alcançar esse objetivo, é importante implementar estratégias eficazes que possam direcionar as ações de melhoria contínua. A seguir, apresentaremos algumas estratégias que podem ser aplicadas para eliminar os desperdícios e otimizar os processos no contexto do Lean Manufacturing:
1. Mapeamento do fluxo de valor (Value Stream Mapping):
O mapeamento do fluxo de valor é uma ferramenta fundamental para identificar oportunidades de melhoria e desperdícios ao longo de todo o processo produtivo. Essa técnica visual permite analisar o fluxo das informações, materiais e atividades, identificando gargalos, tempos de espera e atividades que não agregam valor. Com base nas informações obtidas, é possível desenvolver um plano de ação para eliminar desperdícios e otimizar os processos.
2. Implantação de células de produção ou work cells:
A criação de células de produção ou work cells consiste na organização do espaço de trabalho de forma que as atividades relacionadas a um produto ou família de produtos sejam realizadas em proximidade física, eliminando o transporte desnecessário e reduzindo o tempo de deslocamento. Essa abordagem permite maior interação entre os membros da equipe, agilizando a tomada de decisões e reduzindo o tempo de produção.
3. Implementação de sistemas de gestão visual:
A utilização de sistemas de gestão visual, como quadros de avisos, painéis informativos e indicadores visuais, permite que as informações relacionadas ao desempenho dos processos sejam facilmente acessíveis e compreendidas por toda a equipe. Essa abordagem contribui para a identificação e solução rápida de problemas, além de incentivar a participação e engajamento dos colaboradores.
4. Investimento em automação:
A automação de processos pode ajudar a reduzir desperdícios relacionados a erros humanos, retrabalho e tempo de produção. A utilização de máquinas e equipamentos automatizados permite a execução de atividades de forma mais rápida, precisa e eficiente, aumentando a produtividade e minimizando a ocorrência de defeitos.


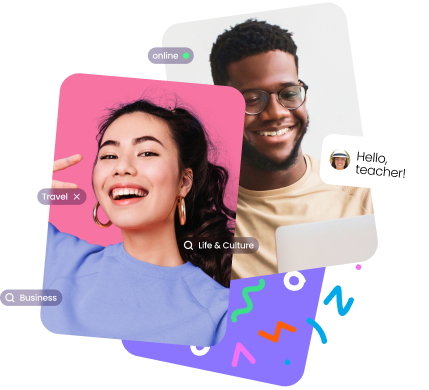
5. Capacitação e treinamento da equipe:
Investir na capacitação e treinamento da equipe é fundamental para eliminar desperdícios causados por habilidades subutilizadas. Ao fornecer a capacitação necessária, os colaboradores serão capazes de desempenhar suas atividades com eficiência, promovendo a melhoria contínua e contribuindo para a eliminação de desperdícios.
Benefícios da redução dos desperdícios no Lean Manufacturing e como maximizar a eficiência:
A redução dos desperdícios no Lean Manufacturing traz uma série de benefícios para as empresas, que vão desde a redução de custos até o aumento da satisfação do cliente. Ao eliminar os desperdícios, é possível maximizar a eficiência do processo produtivo e alcançar resultados mais significativos. A seguir, destacaremos os principais benefícios da redução dos desperdícios no Lean Manufacturing e algumas estratégias para maximizar a eficiência:
1. Redução de custos:
Ao eliminar desperdícios, as empresas são capazes de reduzir custos de produção, armazenagem, transporte e retrabalho. Com a redução dos custos, é possível aumentar a competitividade no mercado, tornando os produtos mais atrativos para os clientes.
2. Aumento da produtividade:
Ao eliminar desperdícios, é possível otimizar o processo produtivo, reduzindo tempos de espera, retrabalho e atividades desnecessárias. Com a melhoria da produtividade, as empresas conseguem produzir mais em menos tempo, atendendo a um maior número de demandas.
3. Melhoria na qualidade dos produtos:
Ao eliminar desperdícios, a empresa reduz a ocorrência de problemas e defeitos nos produtos. Com a melhoria da qualidade, é possível aumentar a satisfação do cliente, fortalecer a reputação da empresa e conquistar a fidelidade dos consumidores.
4. Aumento da flexibilidade do processo produtivo:
Com a eliminação de desperdícios, o processo produtivo se torna mais flexível e adaptável às mudanças do mercado. Isso permite que a empresa consiga responder de forma rápida e eficiente às demandas dos clientes, aproveitando oportunidades e evitando perdas.
5. Melhoria do ambiente de trabalho:
A eliminação de desperdícios contribui para a melhoria das condições de trabalho, reduzindo a sobrecarga e aumentando a segurança dos colaboradores. Um ambiente de trabalho saudável e organizado impacta diretamente na motivação e produtividade da equipe.
Para maximizar a eficiência, é importante combinar a redução dos desperdícios com uma cultura de melhoria contínua, onde todos os colaboradores estejam engajados no processo. Além disso, é essencial utilizar ferramentas e técnicas do Lean Manufacturing, como o Kaizen, o 5S e o PDCA, para promover a gestão e a otimização dos processos de forma constante.
Em suma, a identificação e eliminação dos desperdícios no Lean Manufacturing são fundamentais para alcançar a excelência operacional. Ao implementar estratégias eficazes, as empresas podem reduzir custos, aumentar a produtividade e melhorar a qualidade dos produtos, maximizando sua eficiência e competitividade no mercado.
A Awari é a melhor plataforma para aprender sobre gestão de produtos no Brasil.
Aqui você encontra cursos com aulas ao vivo, mentorias individuais com os melhores profissionais do mercado e suporte de carreira personalizado para dar seu próximo passo profissional e aprender habilidades como Data Science, Data Analytics, Machine Learning e mais.
Já pensou em aprender de maneira individualizada com profissionais que atuam em empresas como Nubank, Amazon e Google? Clique aqui para se inscrever na Awari e começar a construir agora mesmo o próximo capítulo da sua carreira em dados.


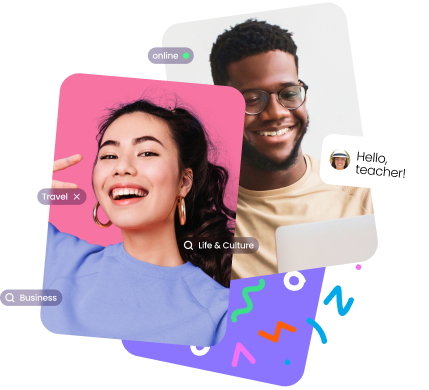